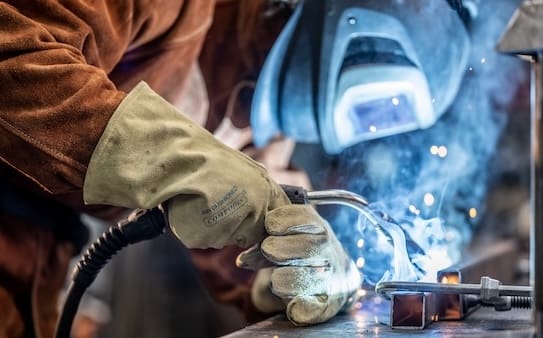
Comparison of welding processes: MIG and MAG welding
MIG welding is a common welding technique found in various industries. It is applied for welding metals like aluminium, nickel, and copper. It is also often referred to as MIG/MAG welding. This is because the only difference between MIG and MAG welding is in the shielding gas, which is used to protect the weld pool. In this article, we will take a closer look at these welding processes.
What is MIG welding?
MIG welding is a relatively simple and, above all, versatile welding technique that uses an inert gas to protect the weld pool. MIG stands for Metal Inert Gas. The welding technique is considered both arc and fusion welding. During MIG welding, a welding wire is mechanically fed continuously during the welding process. A plasma arc is created between this welding wire and the workpiece, with the wire acting as an electrode and simultaneously melting off as a filler metal.
What is MAG welding?
MAG welding operates similarly to the MIG welding process. MAG stands for Metal Active Gas. The difference with MIG welding lies in the shielding gas used. With MIG welding, an inert gas such as argon is used, whereas in MAG welding, an active gas such as carbon dioxide and CO2 is used. An inert shielding gas does not react with the weld pool, while an active gas does react with oxygen. You can read more about MIG MAG gases further on. MAG welding is also known as solid wire welding (process 135), cored wire welding (process 136), or CO2 welding. The technique is used for high-alloy and stainless steels, as well as for welding unalloyed and low-alloy steels and construction steel.
What is the difference between MIG and MAG welding?
Because the welding process is otherwise identical, MIG and MAG welding are also often referred to as one technique. The only real difference in the MIG MAG welding process is the shielding gas used (Inert vs Active). MIG welding is therefore often used when no chemical reaction is desired. It is an ideal technique for welding aluminium and other non-ferrous (non-iron) and inert materials, such as copper. One reason for working with active gas, or to choose MAG welding, is partly because CO2 is cheaper than argon. However, the gas used also affects weld quality and welding speed. Therefore, the choice of gas depends on the material and the desired result.
Why MIG and MAG welding?
MIG and MAG welding are popular techniques that allow you to work fast and achieve high-quality results. They are especially favoured for their flexibility and high deposition rates. MIG welding can be performed both manually and fully by a welding robot and is widely used in places where high productivity is required. By adjusting the wire feed speed, amperage, and voltage of the MIG MAG welding machine or welding gun, it is possible to work with various types of materials, joints, and sizes. In practice, MIG and MAG welding are found in any company that needs to weld high-alloy and stainless steels. This includes sectors like aerospace, offshore, boiler construction, and the automotive industry.
Which gas for MIG welding?
In the MIG/MAG welding process, a weld pool is created to join two metal parts. Without welding gas, the welding wire, the molten material and the weld pool are affected by oxygen and nitrogen from the air. Oxygen will burn the material, while nitrogen creates a porous weld joint. A well-chosen welding gas protects the weld pool from these effects. Which MIG MAG gas is used depends on the desired result and the material to be welded. For MIG welding, argon is the most commonly used gas or a mixture of argon and helium. For MAG welding, a mixture of active gases with inert gases is often used, such as a mixture of argon with oxygen and/or carbon dioxide, or a mixture of argon and hydrogen. Shielding gases with a maximum of 2% nitrogen and 2% CO2 can be used for MAG welding duplex and super duplex steels.
Personal protective equipment for MIG MAG welding
During the MIG MAG welding process, sparks and glowing spatter may occur. These spatters can adhere elsewhere on the workpiece. This is undesirable, especially when the welded part undergoes no further treatment, as is the case with stainless steel. Additionally, spatter is dangerous for the MIG MAG welder. Therefore, good personal protective equipment (PPE) is essential for MIG/MAG welding, such as wearing heat-resistant welding gloves. As a specialist in welding protection, Weldas offers various solutions for the MIG MAG welder with a range of leather welding gloves and A-quality welding clothing.
MIG welding gloves
A number of properties are important for a good welding glove, including safety, comfort, and ease of use. Especially for MIG/MAG welders, wearing welding gloves with the highest degree of protection and good lining is recommended. For this purpose, Weldas has cotton-lined welding gloves and COMFOflex® welding gloves in its range that are type A certified in accordance with the European EN12477 standard. The lining of these gloves ensures a comfortable fit and provides sufficient thermal insulation. The split leather outer shell offers excellent protection against sparks and spatter, making these leather welding gloves perfect for the specific requirements of MIG/MAG welding.
In addition to MIG welding gloves, we also offer TIG welding gloves. These gloves are unlined and often have higher finger sensitivity. This is important for TIG welding, where the welder has to feed the TIG welding wire or rods manually. More about TIG welding and its difference from MIG welding will be covered in another article.
Weldas is also the right address for protective welding clothing for MIG MAG welding. Whether you need welding jackets, aprons or trousers made of leather or flame-retardant cotton, we offer a suitable solution for every welder. View our entire range or contact us for advice.